Fine work
Assembly and testing machine for cleaner diesel engines
Under European regulations, diesel engines are required to emit less nitrogen oxides (NOx). Since 2018, a dosing system has been installed in the exhausts, which adds a urea solution to exhaust gases. The Oldenzaal-based company Vernay has developed a valve for this system. This fluid control solutions specialist develops and manufactures high-quality precision rubber components for the automotive, medical and household appliance industries. For fast, accurate production of this high-precision cylindrical plastic component, Vernay sought a company that could develop an assembly and testing machine. Because of previous collaboration, experience in special machine construction and the ability to meet the high requirements for accuracy, Vernay chose Tuinte.
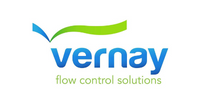
Vernay
Mechanical engineering, Engineering machines
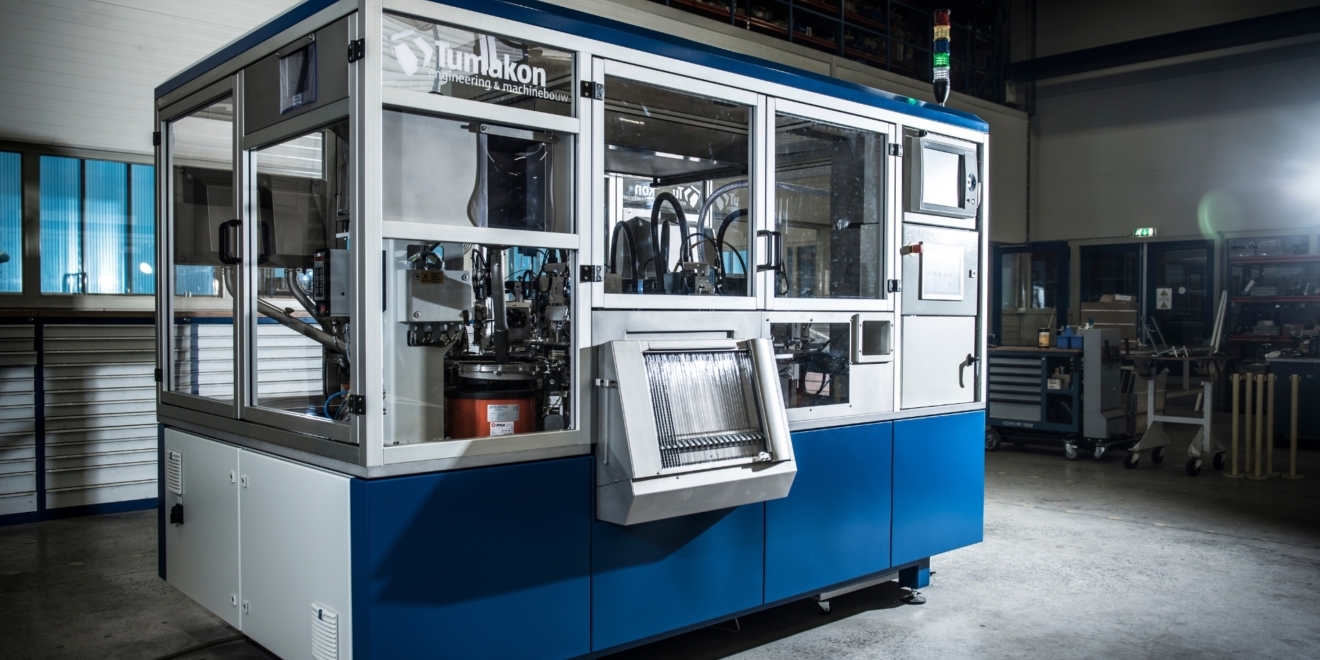
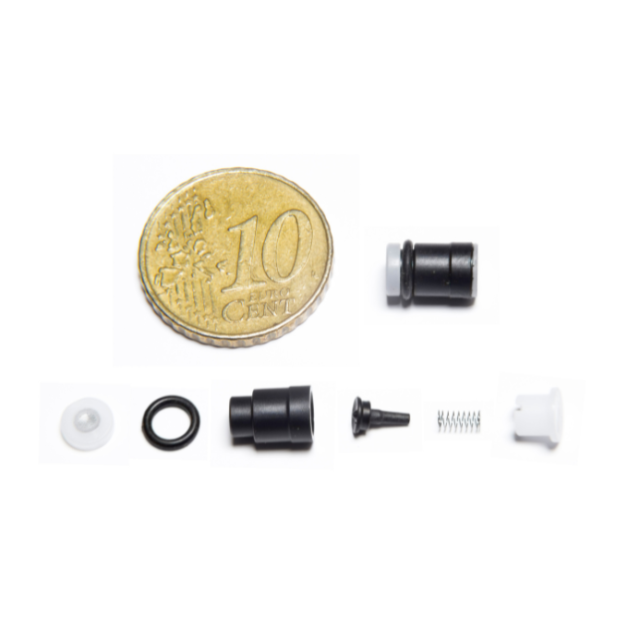
Tight tolerances for completed product
Vernay set requirements for the machine in terms of flow capacity, shut-off behaviour and an installation space of very limited dimensions. The valve is 9 mm by 5.5 mm in diameter and consists of a filter, an o-ring, a spring and a seal. For Tuinte, the challenge was to develop a machine that delivers a complete product every six seconds from six tiny parts. With very tight product tolerances of two microns (micrometres, or thousandths of a millimetre), the parts had to be positioned, assembled, soldered and tested.
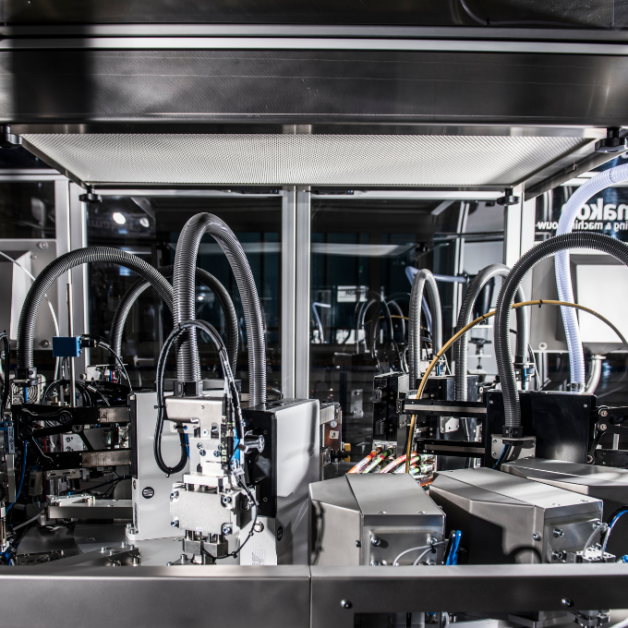
Approach
The automotive industry uses the Production Part Approval Process. This calls for a multidisciplinary approach, preventive work and continuous feedback on the process and on test performance. To meet the specifications and demonstrate the manufacturing process, extensive preliminary research was carried out. Critical and non-critical product and process parameters based on agreed specifications were also defined. On this basis, a PPAP configuration was created and certain critical product steps and processes like welding and assembly were brought forward to ensure proper validation. Criticisms included the steps in which two parts had to be heated with a laser before being pressed together in a very controlled and precise manner. Movement had to be limited because of the high demands on positioning accuracy. As an involved partner, we work with you to develop all specifications in the preliminary stage. So we consulted the supplier on functional welding tests. After all testing and analysis, all welding and test values were recorded in a production database. Four thousand valves were made using a temporary manual assembly process, after which the production process was released.
Tuinte power
The machine was developed entirely in collaboration with Vernay. From the initial contact with the client, there was continuous consultation and feedback with the client and between specialists at Tuinte. Engineers get together with each other, with sales, with operators and technicians. In the design phase, we review, verify and test the specifications internally, analyse the risks and if we see ‘inconsistencies' we look for solutions. Highlighting critical steps at the earliest possible stage saves the customer time and money, and contributes to a higher-quality machine. In addition, Tuinte knows about both engineering and how to build, service and maintain machinery in-house. Technicians involved in assembly and mechanical engineering are therefore involved in the design review. The benefit here is not just smooth cooperation, but also a high level of commitment to delivering the components that we make, test and customise in our own workshop. Setting up and performing tests is also fast and efficient.
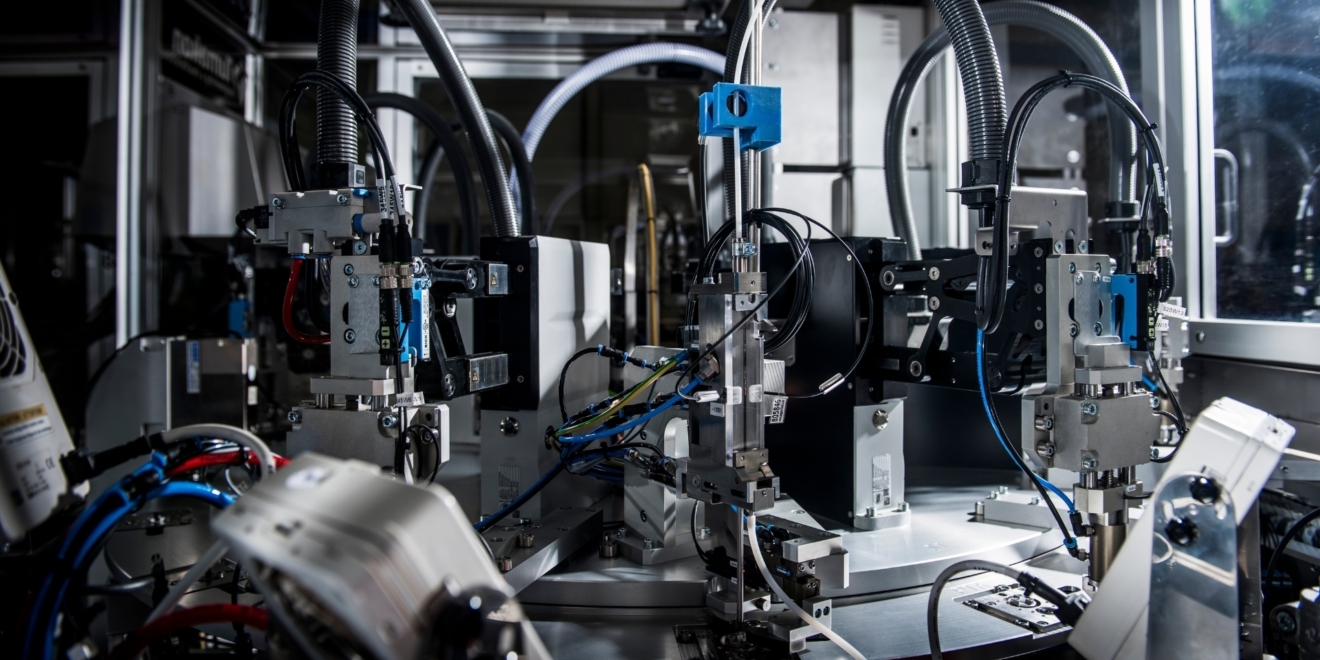